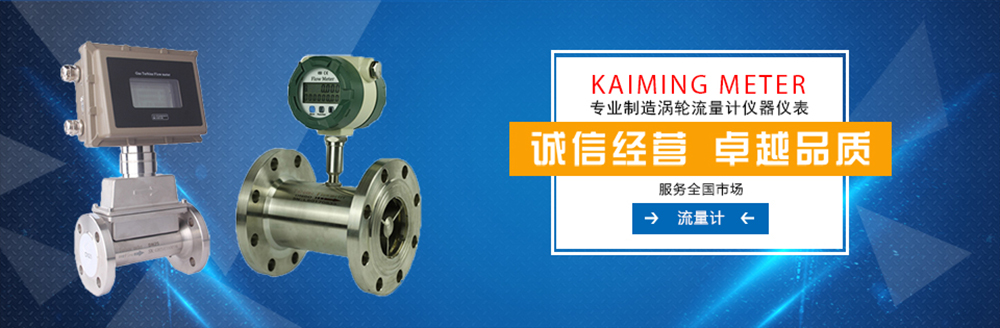
產(chǎn)品目錄
液體渦輪流量計(jì)
液體流量計(jì)
水流量計(jì)
油流量計(jì)
氣體渦輪流量計(jì)
橢圓齒輪流量計(jì)
電磁流量計(jì)
渦街流量計(jì)
蒸汽流量計(jì)
孔板流量計(jì)
旋進(jìn)旋渦流量計(jì)
熱式氣體質(zhì)量流量計(jì)
轉(zhuǎn)子流量計(jì)
浮子流量計(jì)
靶式流量計(jì)
氣體流量計(jì)
超聲波流量計(jì)
磁翻板液位計(jì)
浮子液位計(jì)
浮球液位計(jì)
玻璃管液位計(jì)
雷達(dá)液位計(jì)
超聲波液位計(jì)
投入式液位計(jì)
壓力變送器
差壓變送器
液位變送器
溫度變送器
熱電偶
熱電阻
雙金屬溫度計(jì)
推薦產(chǎn)品
聯(lián)系我們
- 金湖凱銘儀表有限公司
- 聯(lián)系電話:15195518515
- 在線客服:1464856260
- 電話:0517-86801009
- 傳真號(hào)碼:0517-86801007
- 郵箱:1464856260@qq.com
- 網(wǎng)址:http://www.35617.com.cn
- 地址:江蘇省金湖縣理士大道61號(hào)
關(guān)于氣體渦輪流量計(jì)結(jié)構(gòu)與壓損間的關(guān)系
發(fā)布時(shí)間:2021-03-10 06:44:58??點(diǎn)擊次數(shù):2972次
摘要:對DN100氣體渦輪流量計(jì)的關(guān)鍵部件之一前導(dǎo)流器引起的流量計(jì)壓力損失進(jìn)行試驗(yàn)測量和數(shù)值計(jì)算。對比分析兩種不同結(jié)構(gòu)前導(dǎo)流器對壓力損失的影響,發(fā)現(xiàn)前導(dǎo)流器的結(jié)構(gòu)變化不僅影響該部位的氣流速度分布,使當(dāng)?shù)貕毫p失發(fā)生變化,更重要的是對后面各部件內(nèi)的氣體流動(dòng)速度梯度和壓力恢復(fù)也有明顯影響,使總壓損失進(jìn)一步放大或減小。數(shù)值計(jì)算通過分析流動(dòng)參數(shù)的變化從流動(dòng)機(jī)理上解釋了結(jié)構(gòu)與壓損間的關(guān)系。
渦輪流量計(jì)是一種速度式葉輪流量測量儀表,它利用置于流體中的葉輪的旋轉(zhuǎn)角速度與流體流速的正比關(guān)系,通過測量葉輪轉(zhuǎn)速得到流體流速,進(jìn)而得到管道內(nèi)的流量值。渦輪流量計(jì)以其結(jié)構(gòu)簡單、精度高、流通能力大而被大量應(yīng)用于能源動(dòng)力、水利輸運(yùn)和天然氣計(jì)量等工業(yè)領(lǐng)域中。在選用渦輪流量計(jì)時(shí),除要求其準(zhǔn)確度高、量程寬和起始流量小外,壓力損失也是關(guān)鍵指標(biāo)。具有較小壓力損失的渦輪流量計(jì)可減少輸運(yùn)流體的能量消耗,進(jìn)而節(jié)約能源,降低輸送成本。國外較早就開展了對渦輪流量計(jì)的數(shù)值計(jì)算研究,隨著所采用計(jì)算方法和模型精度的提高,在改善渦輪流量計(jì)性能方面取得了顯著進(jìn)步。我國多年來則側(cè)重于提高電信號(hào)轉(zhuǎn)換精度方面的研究,且偏重于試驗(yàn),對流量計(jì)流動(dòng)性能與結(jié)構(gòu)相互影響的理論與數(shù)值研究很少。本文擬通過對傳統(tǒng)和流線形前導(dǎo)流器結(jié)構(gòu)對渦輪流量計(jì)性能影響的數(shù)值模擬計(jì)算,并與試驗(yàn)測量的比較,確定數(shù)值模擬方法的有效性,同時(shí)分析前導(dǎo)流器結(jié)構(gòu)對性能的影響機(jī)理。
1、試驗(yàn)?zāi)P团c測量裝置
1.1流量計(jì)結(jié)構(gòu)與改進(jìn)
渦輪流量計(jì)結(jié)構(gòu)示意圖如圖1所示,主要組件包括前導(dǎo)流器、葉輪、支架以及后管段。流體從機(jī)殼進(jìn)口流入,*先經(jīng)過前導(dǎo)流器,前導(dǎo)流器對流體流動(dòng)有如下兩個(gè)重要作用:
① 收斂作用。氣流在此處由管道流轉(zhuǎn)換為環(huán)形通道流,速度增加而壓力減小,避免流動(dòng)分離產(chǎn)生大的渦旋運(yùn)動(dòng)。
② 導(dǎo)向作用。導(dǎo)流葉片可避免流體自旋而改變對葉輪葉片的作用角度,保證計(jì)量的準(zhǔn)確度。
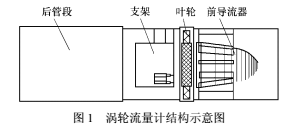
體通過流量計(jì)的壓力損失與介質(zhì)的密度、流速等有關(guān),其計(jì)算公式為
?p=α·ρ·v²/2 (1)
式中,?p為壓力損失,α為壓損系數(shù),ρ為介質(zhì)密度,v為流速。
由于ρ和v為流體流動(dòng)參數(shù),不能隨意增減,因此只能盡量減小壓損系數(shù)α,以達(dá)到降低壓損的目的。壓損系數(shù)除了受流體粘性、管徑及管長等因素影響外,與流量計(jì)內(nèi)部各部件的幾何結(jié)構(gòu)有密切關(guān)系。文獻(xiàn)通過試驗(yàn)發(fā)現(xiàn)葉輪的形線、葉片數(shù)對壓力損失的影響較小(≤3%),因前導(dǎo)流器對流量計(jì)有著重要作用,故將傳統(tǒng)的球形前導(dǎo)流器改進(jìn)為流線形,考察兩者在流動(dòng)減阻方面的不同,進(jìn)而分析對流量計(jì)性能的影響程度。DN100渦輪流量計(jì)改進(jìn)前后的前導(dǎo)流器結(jié)構(gòu)如圖2所示,幾何參數(shù)見下表。
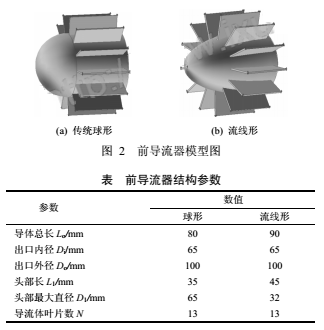
1.2試驗(yàn)裝置
氣體渦輪流量計(jì)的流量與壓力測量裝置如圖3所示。主要包括四部分:測量段部分、穩(wěn)壓罐、標(biāo)準(zhǔn)表、引風(fēng)機(jī)部分。測量段部分包括前直管段、“U”形管或斜管微壓計(jì)、氣體渦輪流量計(jì)、后直管段以及檢測臺(tái);引風(fēng)機(jī)部分包括流量調(diào)節(jié)閥、引風(fēng)機(jī)以及消聲器。
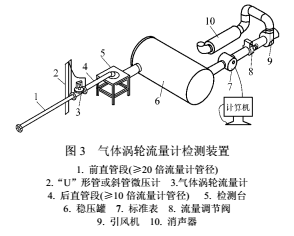
被測流量計(jì)安裝在測量段中,前直管段長度大于20倍被測氣體流量計(jì)管徑,后直管段長度大于10倍流量計(jì)管徑,“U”形管或斜管微壓計(jì)連接在被測流量計(jì)的入口和出口處,用于測量流量計(jì)的壓力損失。標(biāo)準(zhǔn)表為羅茨氣體表,精度0.5級(jí),用于計(jì)量流經(jīng)被測流量計(jì)的氣體流量。標(biāo)準(zhǔn)表與計(jì)算機(jī)連接,由計(jì)算機(jī)進(jìn)行實(shí)時(shí)監(jiān)控,輸出瞬時(shí)流量,并顯示累計(jì)流量值。引風(fēng)機(jī)用于產(chǎn)生管道氣體流量,通過閥門調(diào)節(jié)流量大小,引風(fēng)機(jī)出口端安裝有消聲器以降低噪聲。
2、壓力損失數(shù)值計(jì)算
通過數(shù)值方法模擬兩種前導(dǎo)流器結(jié)構(gòu)下流量計(jì)的內(nèi)部流動(dòng),將模擬結(jié)果與試驗(yàn)宏觀測量參數(shù)進(jìn)行符合度對比,進(jìn)而再對速度、壓力等微觀流動(dòng)參數(shù)進(jìn)行詳細(xì)分析,得出影響壓力損失大小的流動(dòng)規(guī)律。
2.1模型建立與網(wǎng)格劃分
在數(shù)值求解前,*先建立流場的計(jì)算幾何模型。數(shù)值計(jì)算對象與試驗(yàn)流量計(jì)相同,均為DN100氣體渦輪流量計(jì)。按照流量計(jì)的結(jié)構(gòu)特點(diǎn),采用分塊建模方法,將計(jì)算流場分割為前導(dǎo)流、葉輪、支架及后管段(尾流)四個(gè)部分,如圖1所示。
在網(wǎng)格生成過程中,對前導(dǎo)流器和葉輪旋轉(zhuǎn)區(qū)域采用非結(jié)構(gòu)化網(wǎng)格,網(wǎng)格數(shù)為300 000;葉片及導(dǎo)流體壁面處建立5層邊界層網(wǎng)格,*小尺度為0.1mm;支架和尾流部分分區(qū)生成結(jié)構(gòu)化網(wǎng)格,以節(jié)省計(jì)算時(shí)間,網(wǎng)格數(shù)為200 000;對前導(dǎo)流器和葉輪葉片根部附近流動(dòng)變化劇烈的區(qū)域進(jìn)行網(wǎng)格加密處理,以提高網(wǎng)格質(zhì)量,得到較詳細(xì)的流動(dòng)信息。兩種前導(dǎo)流器配以相同的葉輪(葉片數(shù)20)和支架。生成后的計(jì)算網(wǎng)格總數(shù)均為550 000左右。
2.2數(shù)值計(jì)算方法
數(shù)值計(jì)算時(shí),必須建立正確的流動(dòng)物理模型。連續(xù)性方程、N-S運(yùn)動(dòng)方程是描述流體流動(dòng)的基本控制方程組。本文采用將雷諾平均N-S方程組與幾種湍流模型相結(jié)合的數(shù)值求解方法進(jìn)行了求解對比,應(yīng)用雷諾應(yīng)力模型解的收斂性不好,而Spalart-Allmaras模型精度不夠,*終確定采用k–ε兩方程湍流模型解決內(nèi)流方程組的封閉性問題,并達(dá)到求解目的。
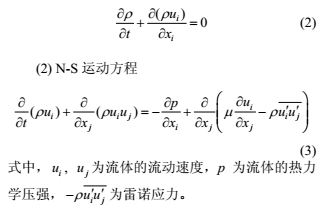
從上述流動(dòng)方程出發(fā),針對流量計(jì)的具體流動(dòng)特點(diǎn)進(jìn)行了如下簡化:將葉輪旋轉(zhuǎn)部分設(shè)定為相對旋轉(zhuǎn)坐標(biāo)系后,流動(dòng)為定常,即不考慮方程中的時(shí)間項(xiàng);考慮到絕大部分流動(dòng)速度小于50m/s,忽略速度變化對密度的影響,即假定流動(dòng)為不可壓。
方程的求解方法采用SIMPLE算法。以“有限體積法”作為流場的數(shù)值離散方法,方程離散過程中采用二階精度的迎風(fēng)差分格式。
由于流場結(jié)構(gòu)復(fù)雜,對湍流雷諾應(yīng)力的模擬采用普適性*好的標(biāo)準(zhǔn)k–ε模型
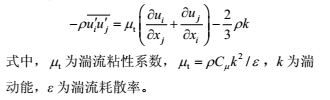
湍動(dòng)能k和湍流耗散率ε則通過對其賦初值后由相應(yīng)的k方程和ε方程求得。
計(jì)算中應(yīng)用的邊界條件如下。
入口:給定相應(yīng)流量下的主流速度值。
出口:滿足質(zhì)量守恒,min=mout。
固壁:壁面函數(shù)法。
葉輪部分采用旋轉(zhuǎn)坐標(biāo)系,給定相應(yīng)流量下的葉輪轉(zhuǎn)速。
3、計(jì)算與試驗(yàn)結(jié)果分析
3.1壓力損失值的比較
圖4為兩種前導(dǎo)流結(jié)構(gòu)下總壓損失與流量的關(guān)系曲線。圖4b為圖4a在量程為0~400m³/h區(qū)間的曲線圖。
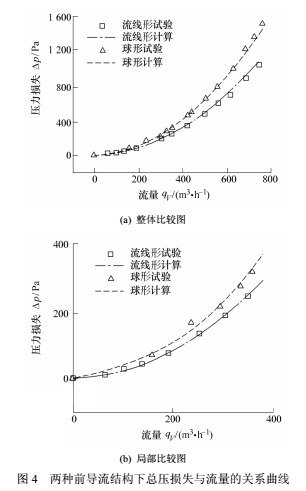
由圖4可知,兩種結(jié)構(gòu)下的計(jì)算與試驗(yàn)值符合很好,誤差在全量程范圍內(nèi)均小于5%。在小流量(≤200 m³/h)區(qū),無論是計(jì)算值還是試驗(yàn)值,兩種結(jié)構(gòu)的壓損值相差非常小,說明前導(dǎo)流結(jié)構(gòu)在流量較小時(shí)對壓損的影響不明顯。隨著流量的增大,結(jié)構(gòu)導(dǎo)致的壓力損失出現(xiàn)了較大差別,明顯看到,流線形與球形的數(shù)值差距越來越大,在*大流量處(約 750 m³/h),球形壓損比流線形增大約30%。
試驗(yàn)和計(jì)算結(jié)果均顯示,氣體流經(jīng)渦輪流量計(jì)的總壓損失隨流量基本呈二次方增長趨勢,即?p=αQ²,這與式(1)是一致的。不同結(jié)構(gòu)的前導(dǎo)流,二次函數(shù)的系數(shù)α不同。對于流線形前導(dǎo)流,該系數(shù)顯然較小。按照式(1)的分析,壓損系數(shù)a代表流動(dòng)過程中各種因素引起能量損失的綜合能力。由此可以推斷,流線形結(jié)構(gòu)更符合流動(dòng)的要求,使流動(dòng)過程中的能量損失被削弱,從而提高了流動(dòng)性能。流量越大,這種改善越明顯。
計(jì)算過程中還發(fā)現(xiàn),在*小流量下(≤30 m³/h),計(jì)算與試驗(yàn)的相對誤差明顯增大。例如在流量為30 m³/h 時(shí),壓力損失測量值為5Pa,而計(jì)算值為2.6Pa,誤差達(dá)48%。分析原因是由斜管微壓計(jì)的測量精度引起,其讀數(shù)誤差為0.5mm,當(dāng)斜管傾斜30°時(shí),產(chǎn)生的相應(yīng)水柱誤差約為3Pa,當(dāng)實(shí)際壓差很小時(shí)容易引起較大的讀數(shù)誤差,鑒于此,本文計(jì)算與試驗(yàn)的比較范圍大于50 m³/h。
3.2數(shù)值模擬結(jié)果流場分析
為進(jìn)一步定量考查前導(dǎo)流器結(jié)構(gòu)對流場特別是對壓力的影響,將兩種結(jié)構(gòu)下數(shù)值模擬流場的壓力與速度分布規(guī)律進(jìn)行了對比分析,從流動(dòng)機(jī)理角度對結(jié)構(gòu)與壓力的關(guān)系給予考查。
圖5為兩種前導(dǎo)流器結(jié)構(gòu)水平中心斷面上的壓力等值線分布,宏觀上,圖5a、5b的壓力變化趨勢是一致的:在前導(dǎo)流器、葉輪和支架部分,壓力均不同程度地降低,由支架進(jìn)入尾流區(qū)后,壓力逐步上升。
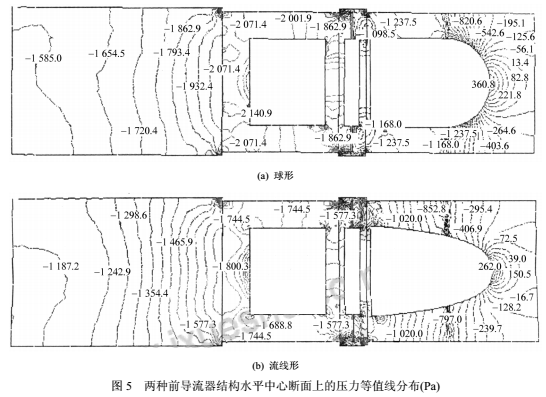
仔細(xì)觀察,兩者在量值上存在較大不同:
①在前導(dǎo)流器部分,球形的前半部壓力變化劇烈,后半部幾乎不變化,流線形的壓力變化體現(xiàn)于整個(gè)流道中,較緩和,結(jié)果使球形(1237.5 Pa)進(jìn)、出口的壓差(入口相對壓力0Pa)明顯高于流線形(1 020.0 Pa),可見流道逐漸收縮有利于減小壓力損失。
②葉輪部分的壓降,球形約為630Pa,流線形為560Pa。在該流域,部分壓能轉(zhuǎn)換為動(dòng)能驅(qū)動(dòng)葉輪旋轉(zhuǎn),流線形壓力損失略低于球形。
③在支架環(huán)形通道中的壓力損失,球形為208.5Pa(支架前端壓力2071.4Pa與末端壓力1 862.9 Pa之差),流線形為167.2Pa(支架前端壓力1 744.5Pa與末端壓力1 577.3Pa之差),也是流線形低于球形。
④由支架出口進(jìn)入突然擴(kuò)張的尾流部分后,氣流減速增壓,在此過程中球形壓力由–2 071.4Pa上升為–1 585.0Pa,增值486.4Pa,流線型由–1 744.5Pa上升為–1 187.2Pa,增值557.3Pa,流線形的壓力回升速度快于球形。
上述四部分壓力變化的疊加體現(xiàn)為渦輪流量計(jì)的總壓損,球形為1 585Pa,流線形1 187Pa,球形比流線形高33%左右。
圖6為與圖5相同位置上的速度等值線分布。在前導(dǎo)流器處,可看出對應(yīng)壓力變化劇烈的區(qū)域,速度變化也較大。球形頭部速度急劇增大、直管段速度幾乎不變的分布趨勢使其中心出口速度(47.0m/s)較大(流線形45.2m/s),在同流量下表明球形前導(dǎo)流器具有較大速度梯度。當(dāng)氣流進(jìn)入尾流部分后,由于流道突擴(kuò),在支架的背面形成明顯的低速渦區(qū),之后管壁附近速度降低,中心區(qū)主流速度回升,速度值被逐漸拉平,對應(yīng)壓力也逐步回升。可看到,至出口斷面,流線形的速度不均勻*大差值為6.0m/s,球形為9.4m/s,即球形的出口速度梯度更大,壓力回升則相應(yīng)較慢。
綜合圖5、6,速度的分布和變化與壓力損失的大小密切相關(guān),流線形前導(dǎo)流器不僅使當(dāng)?shù)氐臍饬魉俣确植驾^球形更均勻(梯度較小),還影響其后的流場速度變化程度,從而使各部分的壓力損失連鎖減小,達(dá)到明顯降低總壓損的目的。
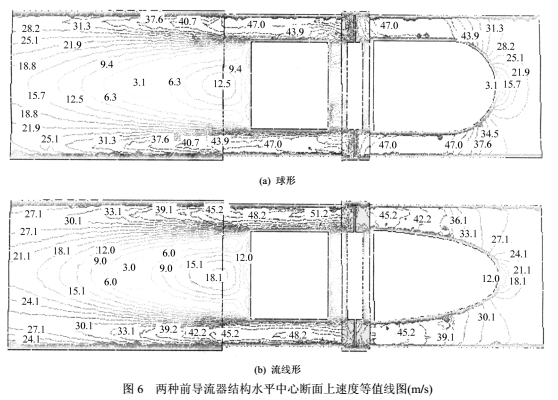
4、結(jié)論
對傳統(tǒng)球形和改進(jìn)的流線形兩種前導(dǎo)流器結(jié)構(gòu)下渦輪流量計(jì)的試驗(yàn)測量和數(shù)值計(jì)算結(jié)果表明,在小流量(≤200 m³/h)下,兩者壓損幾乎相同,即結(jié)構(gòu)對壓力損失的影響很小;隨著流量增大,壓損差值越來越明顯,在*大工作流量(750 m³/h)下,球形壓損比流線形增加了約33%。改進(jìn)后的流線形前導(dǎo)流器通過改善氣流在當(dāng)?shù)丶半S后各部件中的速度和壓力分布,使速度梯度降低,壓力恢復(fù)加快,從而達(dá)到明顯降低總壓損的目的。
計(jì)算與試驗(yàn)的對比結(jié)果顯示,采用數(shù)值計(jì)算方法可以有效地模擬渦輪流量計(jì)內(nèi)部的氣體流動(dòng)從而給出正確的壓力損失值,是進(jìn)一步深入研究渦輪流量計(jì)的可靠工具。
相關(guān)資訊
- 氣體渦輪流量計(jì)安裝直管段要求
- 氣體渦輪流量計(jì)的結(jié)構(gòu)與工作原理
- 氣體渦輪流量計(jì)的產(chǎn)品特點(diǎn)和適用范圍
- 氣體渦輪流量計(jì)選型指南與外形尺寸
- 氣體渦輪流量計(jì)使用環(huán)境
- 氣體渦輪流量計(jì)使用注意事項(xiàng)
- 氣體渦輪流量計(jì)怎么清洗
- 氣體渦輪流量計(jì)適用范圍
- 氣體渦輪流量計(jì)為什么要加油
- 氣體渦輪流量計(jì)波動(dòng)大解決辦法
- 氣體渦輪流量計(jì)安裝距離要求
- 氣體渦輪流量計(jì)安裝注意事項(xiàng)
- 氣體渦輪流量計(jì)應(yīng)用范圍
- 氣體渦輪流量計(jì)常見故障有哪些
- 提高氣體渦輪流量計(jì)精度的方法
- 氣體渦輪流量計(jì)精度等級(jí)
- 氣體渦輪流量計(jì)的技術(shù)參數(shù)
- 氣體渦輪流量計(jì)不準(zhǔn)原因
- 氣體渦輪流量計(jì)的優(yōu)缺點(diǎn)
- 氣體渦輪流量計(jì)的用途
- 氣體渦輪流量計(jì)接線圖
- 氣體渦輪流量計(jì)種類
- 用氣體渦輪流量計(jì)測量天然氣流量
- 氣體渦輪流量計(jì)的優(yōu)點(diǎn)
- 氣體渦輪流量計(jì)使用方法
- 氣體渦輪流量計(jì)的選型表
- 氣體渦輪流量計(jì)結(jié)構(gòu)圖
- 影響氣體渦輪流量計(jì)測量精度的因素及措施
- 氣體渦輪流量計(jì)維護(hù)保養(yǎng)
- 氣體渦輪流量計(jì)特點(diǎn)